Radiative cooling glass coating#
Air conditioning accounts for about 10% of global electricity use, and demand is projected to rise significantly. New approaches like radiative cooling can reduce this energy demand and associated greenhouse gas emissions. Radiative cooling uses materials applied to buildings that reflect sunlight while emitting heat through the atmospheric transparency window (8-13 μm) to outer space (~3K). This can passively cool buildings below ambient temperature. An ideal radiative cooling material would
combine high solar reflection and selective infrared emission for cooling, easy manufacturability at scale, mechanical robustness, and long-term stability under outdoor environmental exposure. A recent paper introduces a new stable, scalable, and low-cost radiative cooling coating using a microporous glass-Al
This notebook simulates the emissivity of the 100 μm thick coating and the result shows that the emissivity (absorptance) of the coating is near unity in the atmospheric transparency window. The design is based on Xinpeng Zhao et al., A solution-processed radiative cooling glass. Science 382, 684-691(2023).
DOI: 10.1126/science.adi2224.
This notebook is contributed by Dr. Yurui Qu.
[1]:
import numpy as np
import matplotlib.pylab as plt
import tidy3d as td
import tidy3d.web as web
from tidy3d.plugins.dispersion import FastDispersionFitter, AdvancedFastFitterParam
Simulation Setup#
The 100 μm thick coating consists of randomly placed Al
[2]:
# Define Paramters
# radius and location of the sphere
radius_Al2O3 = 0.25
radius_SiO2 = 4 # exp is 6um
box_size_xy = 20
box_size_z = 100
vol_Al2O3 = 4/3 * np.pi * np.power(radius_Al2O3,3)
vol_SiO2 = 4/3 * np.pi * np.power(radius_SiO2,3)
vol_box = box_size_xy * box_size_xy * box_size_z
num_Al2O3 = int(np.floor(0.2 * vol_box / vol_Al2O3)) # 20% of volumn is Al2O3
num_SiO2 = int(np.floor(0.3 * vol_box / vol_SiO2)) # 30% of volumn is SiO2
print('num_Al2O3:',num_Al2O3)
print('num_SiO2:',num_SiO2)
num_Al2O3: 122230
num_SiO2: 44
The refractive indices of Al
[3]:
# permittivity of Al2O3
mat_Al2O3 = "misc/mat_Al2O3.csv"
advanced_param = AdvancedFastFitterParam(weights=(1,1))
fitter = FastDispersionFitter.from_file(mat_Al2O3, skiprows=1, delimiter=",")
medium_Al2O3, rms_error = fitter.fit(max_num_poles=6, advanced_param=advanced_param, tolerance_rms=2e-2)
fitter.plot(medium_Al2O3)
plt.show()
[11:43:54] WARNING: Unable to fit with weighted RMS error under fit_fast.py:843 'tolerance_rms' of 0.02
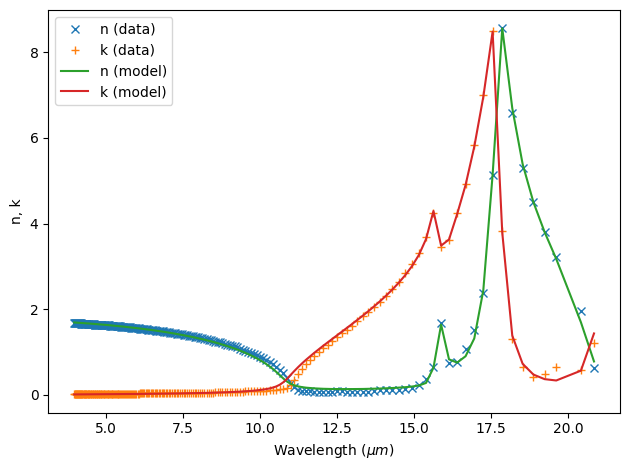
[4]:
mat_SiO2 = "misc/mat_SiO2.csv"
fitter = FastDispersionFitter.from_file(mat_SiO2, skiprows=1, delimiter=",")
medium_SiO2, rms_error = fitter.fit(max_num_poles=8, advanced_param=advanced_param, tolerance_rms=2e-2)
fitter.plot(medium_SiO2)
plt.show()
[11:44:01] WARNING: Unable to fit with weighted RMS error under fit_fast.py:843 'tolerance_rms' of 0.02
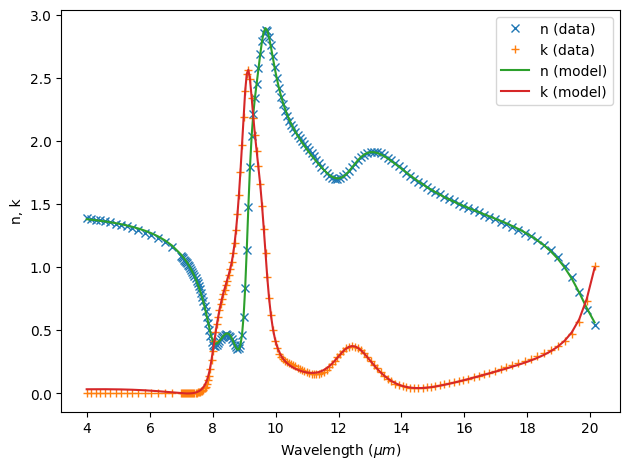
Define some basic simulation parameters.
[5]:
# free space central wavelength
wl_start = 4 # wavelength
wl_end = 20 # wavelength
freq_start = td.C_0 / wl_end
freq_end = td.C_0 / wl_start
freqs = np.linspace(freq_start, freq_end, 100) # freqeucny range of the simulation
freq0 = (freq_start + freq_end)/2 # central frequency
freqw = freq_end - freq_start # width of the frequency range
# distance between the surface of the sphere and the start of the PML layers along each cartesian direction
buffer_PML = 2 * wl_end
buffer_source = 1 * wl_end
# set the domain size in x, y, and z
domain_size_xy = box_size_xy
domain_size_z = buffer_PML + box_size_z + buffer_PML
# construct simulation size array
sim_size = (domain_size_xy, domain_size_xy, domain_size_z)
Next, we generate the randomly placed spheres.
[6]:
# Create random structures
SiO2_geometry = []
Al2O3_geometry = []
geometry = []
for i in range(num_SiO2):
position_xy = (box_size_xy - 2*radius_SiO2) * (np.random.rand(2) - 0.5)
position_z = (box_size_z - 2*radius_SiO2) * (np.random.rand(1) - 0.5)
position = [position_xy[0],position_xy[1],position_z]
sphere = td.Sphere(center=position, radius=radius_SiO2)
SiO2_geometry.append(sphere)
geometry.append(td.Structure(geometry=td.GeometryGroup(geometries=SiO2_geometry), medium=medium_SiO2))
for i in range(num_Al2O3):
position_xy = (box_size_xy - 2*radius_Al2O3) * (np.random.rand(2) - 0.5)
position_z = (box_size_z - 2*radius_Al2O3) * (np.random.rand(1) - 0.5)
position = [position_xy[0],position_xy[1],position_z]
sphere = td.Sphere(center=position, radius=radius_Al2O3)
Al2O3_geometry.append(sphere)
geometry.append(td.Structure(geometry=td.GeometryGroup(geometries=Al2O3_geometry), medium=medium_Al2O3))
geometry = tuple(geometry)
A PlaneWave is defined above the coating layer and two FluxMonitors are defined on both sides of the coating layer to measure transmission and reflection. Lastly, a FieldMonitor is defined to help visualize the field distribution within the coating layer.
[7]:
# add a plane wave source
plane_wave = td.PlaneWave(
source_time=td.GaussianPulse(freq0=freq0, fwidth=0.5 * freqw),
size=(td.inf, td.inf, 0),
center=(0, 0, box_size_z/2 + buffer_source),
direction="-",
pol_angle=0,
)
# add a flux monitor to detect transmission
monitor_t = td.FluxMonitor(
center=[0, 0, -box_size_z/2 - (buffer_source+buffer_PML)/2], size=[td.inf, td.inf, 0], freqs=freqs, name="T"
)
# add a flux monitor to detect reflection
monitor_r = td.FluxMonitor(
center=[0, 0, box_size_z/2 + (buffer_source+buffer_PML)/2], size=[td.inf, td.inf, 0], freqs=freqs, name="R"
)
# add a field monitor to see the field profile at the absorption peak frequency
monitor_field = td.FieldMonitor(
center=[0, 0, 0], size=[td.inf, 0, td.inf], freqs=[freq0], name="field"
)
[11:44:09] WARNING: Default value for the field monitor monitor.py:261 'colocate' setting has changed to 'True' in Tidy3D 2.4.0. All field components will be colocated to the grid boundaries. Set to 'False' to get the raw fields on the Yee grid instead.
Define a Tidy3D Simulation.
[8]:
run_time = 2e-11 # simulation run time
# set up simulation
sim = td.Simulation(
size=sim_size,
grid_spec=td.GridSpec.uniform(dl=wl_start/20),
structures=geometry,
sources=[plane_wave],
monitors=[monitor_t, monitor_r, monitor_field],
run_time=run_time,
boundary_spec=td.BoundarySpec(
x=td.Boundary.periodic(), y=td.Boundary.periodic(), z=td.Boundary.pml()
),
)
Before running the simulation, we can inspect a few things to ensure the simulation is set up correctly. First, plot the source time and frequency spectrum.
[9]:
# Visualize source
plane_wave.source_time.plot(np.linspace(0, run_time/10, 1001))
plt.show()
plane_wave.source_time.plot_spectrum(
times=np.linspace(0, run_time/10, 2000), val="abs"
)
plt.show()
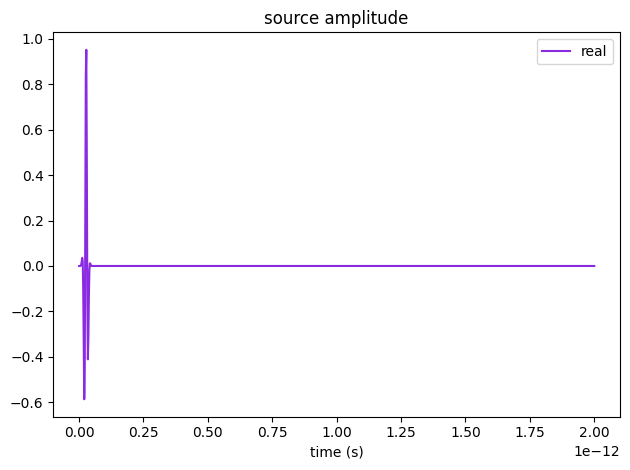
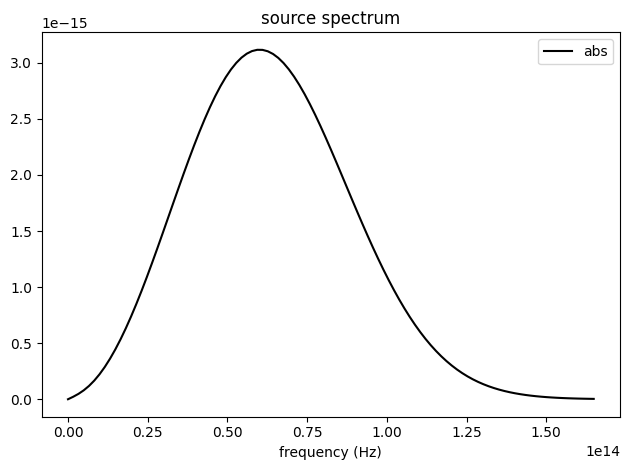
Then, plot the cross sectional view of the simulation.
[10]:
cfig, ax = plt.subplots(1, 2, figsize=(7, 3))
sim.plot(y=0, ax=ax[0])
sim.plot(z=0.1, freq=freq0, ax=ax[1])
plt.show()
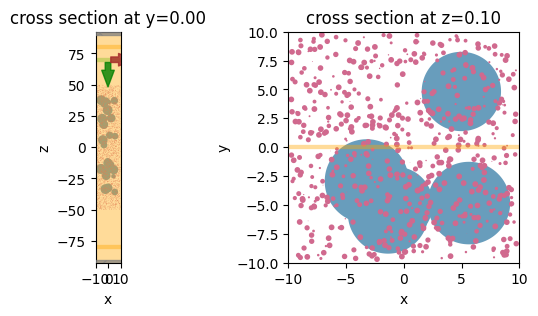
Running the Simulation#
Once we confirm that the simulation is set up correctly, we can upload the simulation and calculate the maximum FlexCredit cost. This step prevents us from submitting large simulations by mistake.
[11]:
task_id = web.upload(sim, task_name="Simulation")
estimated_cost = web.estimate_cost(task_id)
print(f'The estimated maximum cost is {estimated_cost:.3f} Flex Credits.')
View task using web UI at webapi.py:190 'https://tidy3d.simulation.cloud/workbench?taskId=fdve- ac012451-a2eb-42a8-9a30-22c8e35abfd4v1'.
The estimated maximum cost is 0.726 Flex Credits.
The cost seems reasonably so we start the task and monitor its status. After the simulation is complete, we can print out the real cost.
[12]:
web.start(task_id)
web.monitor(task_id, verbose=True)
import time
time.sleep(20)
print("Billed flex unit cost: ", web.real_cost(task_id))
sim_data = web.load(task_id, path="data/cooling.hdf5")
# Show the output of the log file
print(sim_data.log)
Billed flex unit cost: 0.2613711908533915
Simulation domain Nx, Ny, Nz: [100, 100, 924]
Applied symmetries: (0, 0, 0)
Number of computational grid points: 9.2600e+06.
Using subpixel averaging: True
Number of time steps: 5.2452e+04
Automatic shutoff factor: 1.00e-05
Time step (s): 3.8131e-16
Compute source modes time (s): 22.3489
Compute monitor modes time (s): 2.3306
Rest of setup time (s): 34.0244
Running solver for 52452 time steps...
- Time step 70 / time 2.67e-14s ( 0 % done), field decay: 1.00e+00
- Time step 2098 / time 8.00e-13s ( 4 % done), field decay: 4.25e-02
- Time step 4196 / time 1.60e-12s ( 8 % done), field decay: 9.84e-04
- Time step 6294 / time 2.40e-12s ( 12 % done), field decay: 1.59e-04
- Time step 8392 / time 3.20e-12s ( 16 % done), field decay: 5.67e-05
- Time step 10490 / time 4.00e-12s ( 20 % done), field decay: 2.71e-05
- Time step 12588 / time 4.80e-12s ( 24 % done), field decay: 1.61e-05
- Time step 14686 / time 5.60e-12s ( 28 % done), field decay: 1.30e-05
- Time step 16784 / time 6.40e-12s ( 32 % done), field decay: 1.08e-05
- Time step 18882 / time 7.20e-12s ( 36 % done), field decay: 7.80e-06
Field decay smaller than shutoff factor, exiting solver.
Solver time (s): 126.6290
Data write time (s): 0.0118
Result Visualization#
After the simulation is complete, we will plot the transmission, reflection, and absorption spectra. The result shows that the absorption is nearly 100% in the atmospheric transparency window of 8-13 μm. Furthermore, based on Kirchhoff’s law of thermal radiation, the emissivity of a material is equal to its absorptance, we know that the infrared emissivity of the coating layer is close to unity.
Lastly, we can plot the field distribution within the coating layer. The plot shows that the electromagnetic energy is strongly absorbed as it propagates into the layer.
[13]:
# Result Visualization
R = sim_data["R"].flux
T = -sim_data["T"].flux
A = 1 - R - T
plt.plot(td.C_0 /freqs, R, td.C_0 /freqs, T, td.C_0 /freqs, A)
# Save the absorption spectrum as as a .txt file
np.savetxt('data/Abs_4-20um.txt', (np.transpose((td.C_0 /freqs, A))))
plt.xlabel("Wavelength (μm)")
plt.ylim(0, 1)
plt.legend(("R", "T", "A"))
plt.show()
ax = sim_data.plot_field(field_monitor_name="field", field_name="E", val="abs^2")
ax.set_aspect('auto')
plt.show()
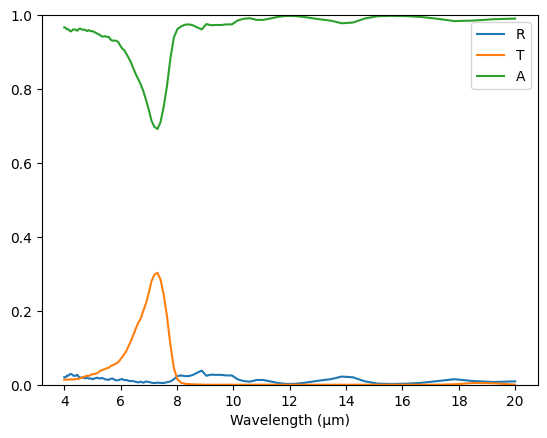
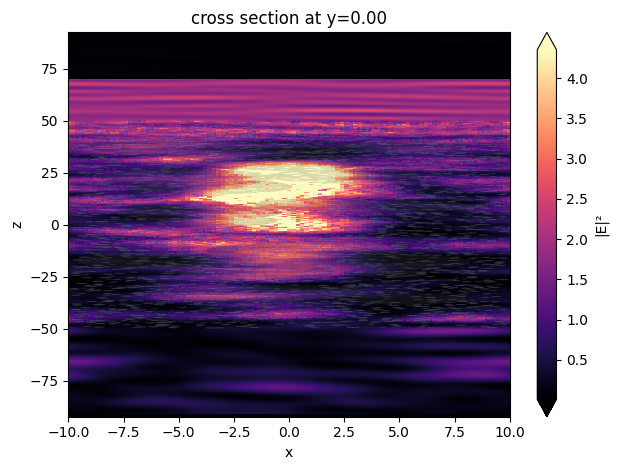
[ ]: