Euler waveguide bend#
Efficiently routing light in a densely packed photonic chip has been a central topic in the photonic industry. This inevitably requires the use of waveguide bends of various angles and radii. Electromagnetic waves can travel in straight waveguides for a long distance with very little loss. However, when it enters a waveguide bend, significant reflection and leakage could occur.
The most common waveguide bends are circular bends. A silicon waveguide bend typically has a loss in the order of 0.01 dB. This loss is sufficiently small for many applications. However, in cases where a large number of bends are used, the total loss due to the bends can be quite large. Therefore, new methods to reduce bending loss is needed. Recently, T. Fujisawa et al. demonstrated that a waveguide bend following the clothoid curve, also known as the Euler bend, yields a much lower loss compared to a circular bend due to its smooth curvature transition. In this example notebook, we model a 90 degree Euler waveguide bend and compare its loss to a conventional circular bend. The loss of the Euler waveguide bend is found to be several times smaller compared to the circular bend of the same effective radius at the telecom wavelength.
For more integrated photonic examples such as the 8-Channel mode and polarization de-multiplexer, the broadband bi-level taper polarization rotator-splitter, and the broadband directional coupler, please visit our examples page.
[1]:
import numpy as np
import matplotlib.pyplot as plt
import scipy.integrate as integrate
from scipy.optimize import fsolve
import gdstk
import tidy3d as td
import tidy3d.web as web
Clothoid Bend vs. Circular Bend#
The expression for a clothoid curve (Euler curve) whose starting point is at the origin is given by
and
where
In this example notebook, we model waveguide bends with a 4
[2]:
R_eff = 4 # effective radius of the bend
A = 2.4 # clothoid parameter
An important step in constructing the Euler bend is to determine
[3]:
L_max = 0 # starting point of L_max
precision = 0.05 # increasement of L_max at each iteration
tolerance = 0.01 # difference tolerance of the derivatives
# determine L_max
while True:
L_max = L_max + precision # update L_max
Ls = np.linspace(0, L_max, 50) # L at (x1,y1)
x1 = np.zeros(len(Ls)) # x coordinate of the clothoid curve
y1 = np.zeros(len(Ls)) # y coordinate of the clothoid curve
# compute x1 and y1 using the above integral equations
for i, L in enumerate(Ls):
y1[i], err = integrate.quad(lambda theta: A * np.sin(theta**2 / 2), 0, L / A)
x1[i], err = integrate.quad(lambda theta: A * np.cos(theta**2 / 2), 0, L / A)
# compute the derivative at L_max
k = -(x1[-1] - x1[-2]) / (y1[-1] - y1[-2])
xp = x1[-1]
yp = y1[-1]
# check if the derivative is continuous at L_max
R = np.sqrt(
((R_eff + k * xp - yp) / (k + 1) - xp) ** 2
+ (-(R_eff + k * xp - yp) / (k + 1) + R_eff - yp) ** 2
)
if np.abs(R - A**2 / L_max) < tolerance:
break
# after L_max is determined, R_min is also determined
R_min = A**2 / L_max
After determining the first piece of the clothoid curve, the second piece can be obtained simply by mirroring it with respect to
[4]:
# getting the coordinates of the second clothoid curve by mirroring the first curve with respect to y=-x+R_eff
x3 = np.flipud(R_eff - y1)
y3 = np.flipud(R_eff - x1)
The last step is to determine the circular curve connecting the clothoid curves. This can be done simply by enforcing a circle fsolve
function from scipy.optimize
to solve for
[5]:
# solve for the parameters of the circular curve
def circle(var):
a = var[0]
b = var[1]
Func = np.empty((2))
Func[0] = (xp - a) ** 2 + (yp - b) ** 2 - R_min**2
Func[1] = (R_eff - yp - a) ** 2 + (R_eff - xp - b) ** 2 - R_min**2
return Func
a, b = fsolve(circle, (0, R_eff))
# calculate the coordinates of the circular curve
x2 = np.linspace(xp + 0.01, R_eff - yp - 0.01, 50)
y2 = -np.sqrt(R_min**2 - (x2 - a) ** 2) + b
Now we have obtained the coordinates of the whole Euler bend, we can plot it with a conventional circular bend to see the difference. Compared to the circular bend, we can see the Euler bend has a smaller curvature at
[6]:
# obtain the coordinates of the whole Euler bend by concatenating three pieces together
x_euler = np.concatenate((x1, x2, x3))
y_euler = np.concatenate((y1, y2, y3))
# the conventional circular bend is simply given by a circle
x_circle = np.linspace(0, R_eff, 100)
y_circle = -np.sqrt(R_eff**2 - (x_circle) ** 2) + R_eff
# plotting the shapes of the Euler bend and the circular bend
plt.plot(x_euler, y_euler, label="Euler bend")
plt.plot(x_circle, y_circle, "--", label="Circular bend")
plt.axis("equal")
plt.ylim(-1, R_eff + 1)
plt.legend()
plt.show()
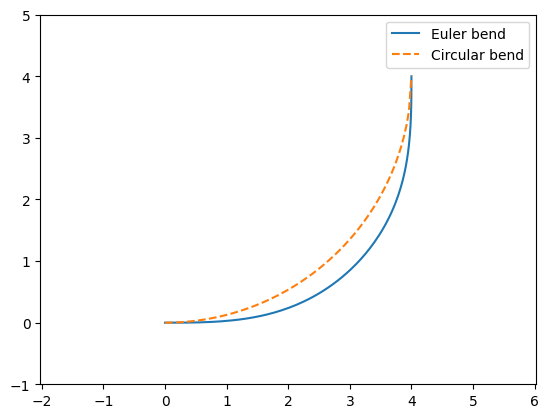
Loss of a Circular Bend#
We first simulate a circular waveguide bend as a baseline reference. Then in the next section, we will simulate an Euler bend and compare their losses quantitatively. Both simulations share the same parameters and simulation setup. The only difference is the bend structure.
[7]:
lda0 = 1.55 # central wavelength
freq0 = td.C_0 / lda0 # central frequency
ldas = np.linspace(1.5, 1.6, 100) # simulation wavelength range
freqs = td.C_0 / ldas # simulation wavelength range
fwidth = 0.5 * (np.max(freqs) - np.min(freqs)) # frequency width of the souce
[8]:
t = 0.21 # thickness of the waveguide
w = 0.4 # width of the waveguide
inf_eff = 100 # effective infinity of the simulation
buffer = 1 # buffer distance
The silicon waveguide on the oxide substrate has an oxide top cladding. Therefore, we will define two materials for the simulations. Both are modeled as non-dispersive in this case.
[9]:
n_si = 3.476 # silicon refractive index
si = td.Medium(permittivity=n_si**2)
n_sio2 = 1.444 # silicon oxide refractive index
sio2 = td.Medium(permittivity=n_sio2**2)
In the previous section, we obtained the coordinates that describe the Euler bend and the circular bend. To construct the 3D waveguide bend structure, we define a helper function here. We make use of gdstk
to convert the coordinates of a bend to a Tidy3D PolySlab.
[10]:
# function that takes the x and y coordinates of a curve and returns a waveguide bend structure with a given width and thickness
def line_to_structure(x, y, w, t):
cell = gdstk.Cell("bend") # define a gds cell
# add points to include the input and output straght waveguides
x = np.insert(x, 0, -inf_eff)
x = np.append(x, R_eff)
y = np.insert(y,0,0)
y = np.append(y, inf_eff)
cell.add(gdstk.FlexPath(x + 1j * y, w, layer=1, datatype=0)) # add path to cell
# define structure from cell
bend = td.Structure(
geometry=td.PolySlab.from_gds(
cell,
gds_layer=1,
axis=2,
slab_bounds=(0, t),
)[0],
medium=si
)
return bend
Use the line_to_structure
function to create the circular bend structure.
[11]:
circular_bend = line_to_structure(x_circle, y_circle, w, t)
Defined a ModeSource for excitation, a ModeMonitor for detecting transmission, and a FieldMonitor to visualize the field propagation and leakage in the bend. The fundamental TE mode is excited
in the input waveguide. All boundaries are set to PML for efficient absorption of the outgoing radiation. Using an automatic nonuniform grid is the most efficient and convenient. We set min_steps_per_wvl=20
to achieve a very accurate result while still keeping the simulation cost at a minimum.
[12]:
# add a mode source that launches the fundamental te mode
mode_spec = td.ModeSpec(num_modes=1, target_neff=n_si)
mode_source = td.ModeSource(
center=(-buffer, 0, t / 2),
size=(0, 4 * w, 6 * t),
source_time=td.GaussianPulse(freq0=freq0, fwidth=fwidth),
direction="+",
mode_spec=mode_spec,
mode_index=0,
)
# add a mode monitor to measure transmission
mode_monitor = td.ModeMonitor(
center=(R_eff, R_eff + buffer, t / 2),
size=(4 * w, 0, 6 * t),
freqs=freqs,
mode_spec=mode_spec,
name="mode",
)
# add a field monitor to visualize field propagation and leakage in the bend
field_monitor = td.FieldMonitor(
center=(R_eff / 2, R_eff / 2, t / 2),
size=(td.inf, td.inf, 0),
freqs=[freq0],
colocate=True,
name="field",
)
run_time = 5e-13 # simulation run time
# define simulation
sim = td.Simulation(
center=(R_eff / 2, R_eff / 2, t / 2),
size=(R_eff + 2 * w + lda0, R_eff + 2 * w + lda0, 10 * t),
grid_spec=td.GridSpec.auto(min_steps_per_wvl=20, wavelength=lda0),
structures=[circular_bend],
sources=[mode_source],
monitors=[mode_monitor, field_monitor],
run_time=run_time,
boundary_spec=td.BoundarySpec.all_sides(
boundary=td.PML()
), # pml is applied in all boundaries
medium=sio2,
) # background medium is set to sio2 because of the substrate and upper cladding
# visualize the circular bend structure
sim.plot(z=0)
plt.show()
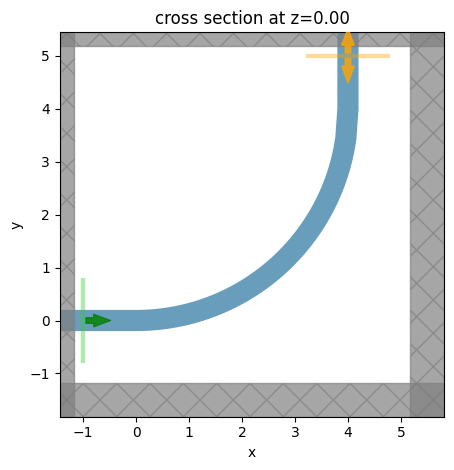
Submit the simulation job to the server.
[13]:
job = web.Job(simulation=sim, task_name="circular_bend")
sim_data_circular = job.run(path="data/simulation_data_circular.hdf5")
View task using web UI at webapi.py:190 'https://tidy3d.simulation.cloud/workbench?taskId=fdve- 50a6b1cd-cf59-4085-8e56-3b932fe1cc9cv1'.
After the simulation is complete, we first plot the bending loss as a function of wavelength. The circular bend exhibits a bending loss ~0.015 dB, which is already pretty low. In many applications, circular waveguide bends can meet the requirement.
[14]:
# extract the transmission data from the mode monitor
amp = sim_data_circular["mode"].amps.sel(mode_index=0, direction="+")
T_circular = np.abs(amp)**2
# plot the bending loss as a function of wavelength
plt.plot(ldas, -10 * np.log10(T_circular))
plt.xlim(1.5, 1.6)
plt.ylim(0, 0.03)
plt.xlabel("Wavelength ($\mu m$)")
plt.ylabel("Bending loss (dB)")
plt.show()
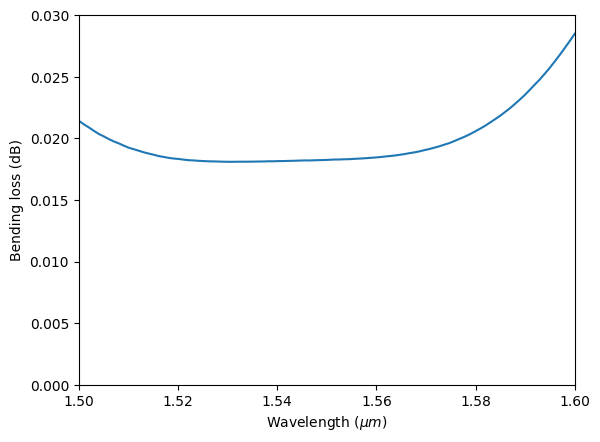
To inspect where the loss occurs in the bend, we plot the field intensity in log scale.
The energy leakage manifests as field intensity outside of the waveguide. Here we can see that leakage occurs around the transition region where the straight waveguide meets the circular waveguide. This is due to the abrupt change of curvature.
[15]:
sim_data_circular.plot_field(
field_monitor_name="field",
field_name="E",
val="abs",
scale="dB",
vmin=-20,
vmax=30,
)
plt.show()
/home/momchil/miniconda3/envs/tidy3d-docs/lib/python3.9/site-packages/xarray/core/computation.py:769: RuntimeWarning: divide by zero encountered in log10
result_data = func(*input_data)
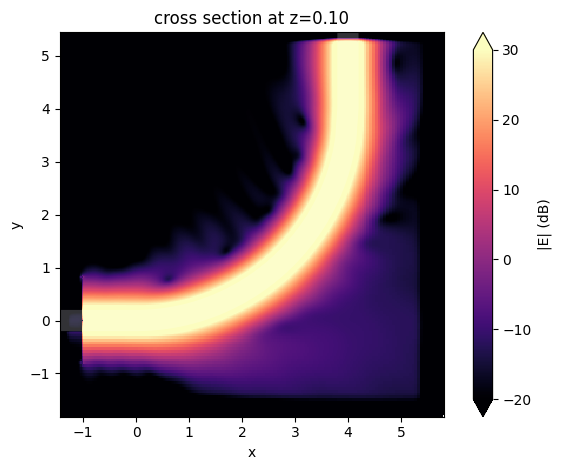
Loss of an Euler Bend#
Next, we perform a similar simulation for the Euler waveguide bend and compare the results to the circular bend. The Euler waveguide bend structure is made by using the line_to_structure
function we defined earlier. Since the simulation setup is the same as the previous one with the only difference being the structures, we can simply copy the previous simulation and update the structures.
[16]:
# create the euler waveguide bend structure
euler_bend = line_to_structure(x_euler, y_euler, w, t)
# construct the simulation by copying the previous simulation and updating the structure
sim = sim.copy(update={"structures": [euler_bend]})
# visualize the euler bend structure
sim.plot(z=0)
plt.show()
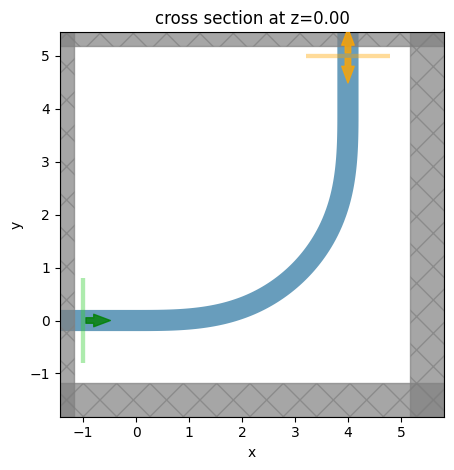
Submit the simulation to the server.
[17]:
job = web.Job(simulation=sim, task_name="circular_bend")
sim_data_euler = job.run(path="data/simulation_data_euler.hdf5")
View task using web UI at webapi.py:190 'https://tidy3d.simulation.cloud/workbench?taskId=fdve- f8989cca-75be-4f48-9481-3fec7d950b06v1'.
After the simulation is complete, we plot the bending loss of the Euler bend against that of the circular bend. Here we see that the Euler bend has a lower loss ~0.005 dB. In terms of absolute loss, both bends are very good. However, when a large number of waveguide bends are used in an integrated photonic circuit, the advantage of the Euler bend can be quite significant.
[18]:
# extract the transmission data from the mode monitor
amp = sim_data_euler["mode"].amps.sel(mode_index=0, direction="+")
T_euler = np.abs(amp)**2
# plotting the losses
plt.plot(ldas, -10 * np.log10(T_circular), label="Circular bend")
plt.plot(ldas, -10 * np.log10(T_euler), label="Euler bend")
plt.xlim(1.5, 1.6)
plt.ylim(0, 0.03)
plt.xlabel("Wavelength ($\mu m$)")
plt.ylabel("Bending loss (dB)")
plt.legend()
plt.show()
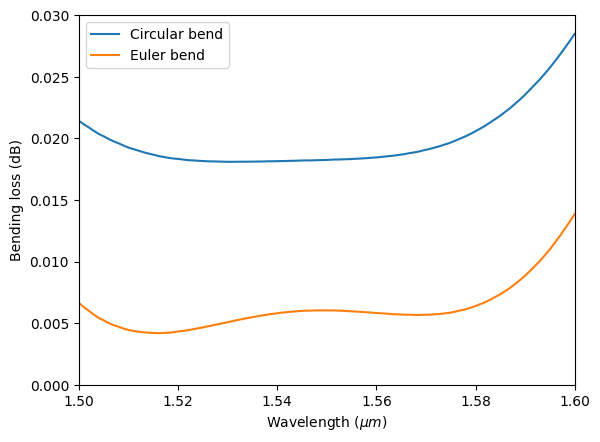
Similarly, we plot the field intensity in log scale. From the plot, we can see that the leakage around the transition regions is indeed reduced. This is due to the fact that the curvature of the Euler curve varies smoothly.
[19]:
sim_data_euler.plot_field(
field_monitor_name="field",
field_name="E",
val="abs",
scale="dB",
vmin=-20,
vmax=30,
)
plt.show()
/home/momchil/miniconda3/envs/tidy3d-docs/lib/python3.9/site-packages/xarray/core/computation.py:769: RuntimeWarning: divide by zero encountered in log10
result_data = func(*input_data)
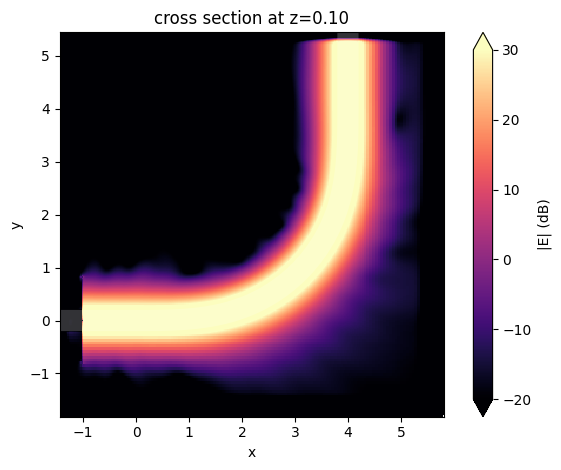
[ ]: